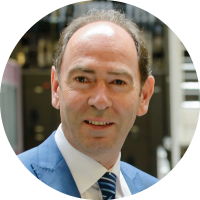
Professor Denis Dowling
Director, I-Form
Constant supply of key materials used in the manufacture of essential products is no longer a given. Saving waste in the fabrication process is therefore more vital than ever.
Critical raw materials including lithium and tungsten — defined by the EU as ‘economically and strategically important for the European economy’ — are used to make a range of essential products. However, there is a growing threat to the continuous supply of these and other raw materials.
Critical materials supply challenges
To maintain and establish a secure and sustainable supply, the EU’s Critical Raw Materials Act came into force in May, listing 34 critical materials and including raw materials recycling targets. Massive demand from a growing middle class, particularly in India and China, is one reason for this disruption in supply.
“Geopolitics is another,” says Professor Denis Dowling, Director of I-Form, the Advanced Manufacturing Research Centre funded by Taighde Éireann – Research Ireland. Headquartered at University College Dublin, the Centre is a partnership between nine academic institutes across Ireland, working with industry to achieve a step change in manufacturing process efficiency and sustainability.
The rare earth
element neodymium
is now in big demand.
“For example, the rare earth element neodymium is now in big demand as it’s used in production of magnets found in electric vehicles and wind turbine motors. Yet, approximately 87% of the world’s rare earths are produced in China, which recently applied sweeping restrictions on their export.”
Consequently, prices have increased in global markets. China is also the world’s biggest producer of titanium, which is used in many manufacturing areas, including aircraft and life-saving medical devices, such as stents. “A question over its supply will dictate where products like these are manufactured,” says Professor Dowling. “It leaves Europe quite exposed.”
Developing academic and research talent for manufacturing
I-Form works with a broad range of manufacturing companies, including those in the clean energy and medical device sectors, on research that aims to minimise critical raw material waste during fabrication. Research areas include materials modelling and AI-based process feedback tools for real-time defect identification. Adoption of these tools has yielded impressive results. One industry partner reported a 90% reduction in experiments needed to achieve optimum product performance, with associated material and energy savings.
Another focus for I-Form is the development of the academic and research talent that will be crucial for Ireland’s manufacturing sustainability. “During our first six-year period, approximately 130 PhD and postdoc researchers were working within the Centre,” says Professor Dowling. “Those researchers have gained a combination of materials and digital skills and, for the most part, will go directly into industry. Along with the work we’re doing to help companies better use materials and minimise waste, we’re having a significant impact on the talent pipeline.”