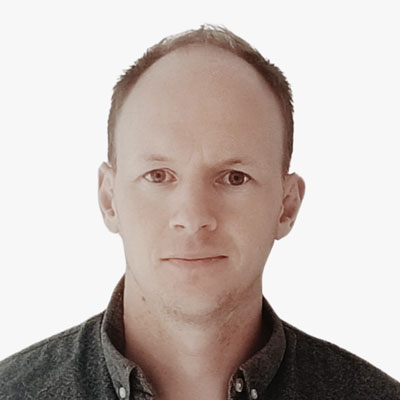
Alan Kavanagh
Senior Digitalisation Programme Manager, Irish Manufacturing Research
The highest-performing companies in the world run on data. Many manufacturing organisations are still facing challenges in data integration across their systems, inhibiting their competitiveness in the quickly evolving era of Industry 4.0.
Data generated from manufacturing operational technology (OT) systems — industrial equipment, sensors, production systems etc. — are some of the fastest-growing data subsets in the world. The opportunity to drive transformational change by refining this data into actionable information, particularly utilising AI, is significant. The challenge faced by manufacturers is how they collect and prepare their data, at scale, to fuel the coming wave of AI innovation.
Architecting data pipelines
No two factories are the same, particularly when it comes to data. A typical factory digital footprint is made up of a fragmented mix of equipment, vendors, software platforms, communication protocols and more. Traditional approaches to connecting assets and collecting data from OT and IT systems have required mostly monolithic, proprietary stacks of software, often with closed architectures from specialist service providers. These ‘point-to-point’ linear integration approaches, transferring data from the shop floor through OT/IT layers to enterprise or cloud solutions, have been the foundation of manufacturing IT and OT systems for decades.
No two factories are the same,
particularly when it comes to data.
This proven approach has advantages in security and reliability but can often lack flexibility and ability to scale. Moreover, it can be costly to develop and alter. Seeking change, industry innovators and disruptors are pioneering other approaches. Functionally driven, open factory data architectures are now becoming an important foundation for successful digital transformation.
Emerging OT systems and security challenges
Among the trending OT architectures, decoupled messaging-based systems are gaining popularity. These architectures allow for all equipment, people and systems (nodes) in the factory to become data ‘publishers’ and ‘subscribers,’ creating massive flexibility and scalability.
New architectures offer advantages but face challenges in widespread adoption, especially in addressing cyber security risks and ensuring compliance with strict regulatory standards. Irish Manufacturing Research (IMR), along with its ecosystem of partners, is enhancing its digital factory capabilities to showcase the art of the possible in this critical area for Irish manufacturing.