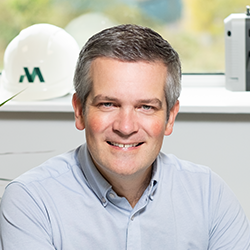
JP Kelly
Associate Director, Murphy Geospatial
In the ever-evolving landscape of manufacturing, the transition to Industry 4.0 stands as a crucial milestone.
With eyes on Industry 5.0 already, a challenge looms — the imperative to get it right within 4.0 before embarking on this new venture. At the heart of this pivotal juncture lies the critical issue of data: its volume, quality and, most importantly, standardisation.
Processing good quality data
The manufacturing sector finds itself grappling with a deluge of data — a veritable ocean of information generated by connected devices, machines and systems. While the potential of this data is immense, the pressing question arises: What good is data if it’s bad data? The efficacy of Industry 4.0 hinges on the reliability and standardisation of the information flowing through the digital veins of smart factories.
The need to bring every stakeholder along on this journey is paramount to every manufacturing company and its ability to compete globally. Before venturing into Industry 5.0, it is imperative to iron out wrinkles in current technological implementations and data usage, creating a foundation for seamless progression.
Before venturing into Industry 5.0, it is imperative to iron out wrinkles in current technological implementations and data usage, creating a foundation for seamless progression.
Merging the physical and digital realms
The future envisions a manufacturing ecosystem where the Internet of Things (IoT) and a network of sensors provide real-time insights into facilities; an intuitive digital twin serves as the nexus between the physical and digital realms. This promises heightened efficiency, waste reduction and error elimination.
However, this is contingent on the standardisation and governance of data that is increasing by the nanosecond. Standardisation becomes the linchpin, ensuring that data speaks a common language across diverse systems.
Standardised data enables resilience
This standardisation is something we strive for in the geospatial sector: a single source of truth from which understanding can be gathered. The informed use of geospatial data enables the integration of smart machinery and smart factories — propelled by standardised data — promising to enhance efficiency and productivity across the entire value chain.
It’s crucial the roadmap to Industry 5.0 is paved with the meticulous standardisation of data, ensuring that our manufacturing future is not only technologically advanced but also resilient and adaptive.