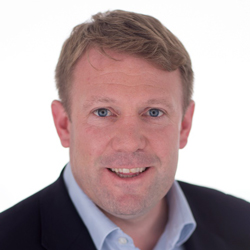
Shane Doyle
Senior Vice President and Head of Operations, Alexion
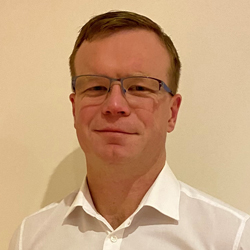
Michael Teehan
Vice President and Head of Integrated Manufacturing, Alexion
Continuous improvement projects accelerate sustainability efforts to help achieve climate targets.
In 2019, Alexion proactively engaged an independent consultant who conducted a comprehensive environmental, health and safety (EHS) audit at all its manufacturing sites and research and development facilities worldwide to validate what was working well and where there were opportunities to drive enhancements.
The audit identified areas for improvement and, subsequently, each location developed specific action plans and focused on continuous improvement throughout 2020-21.
Commitment to sustainability goals
“Alexion is committed to reducing our environmental footprint and ensuring the health and safety of our people and the communities where we call home,” Doyle adds.
The company is governed by a strong environmental, health and safety Policy, which is governed by our commitment to sustainability.
“Our environmental management system follows widely accepted global standards, including ISO 14001, and is backed by an extensive suite of in-house EHS standards,” Doyle says.
“We’ve been focused on sustainability for several years and wanted to better understand how we could accelerate our efforts,” Doyle says. “We took these findings to heart and are making changes today to further advance our sustainability initiatives in the future.”
Alexion focused on bolstering its EHS management review process and taking actions aimed at scaling and standardising internal reporting elements and improving in compliance activities to ensure continuous improvements could take place.
Putting review into practice
The Clean in Place (CIP) process at Alexion’s Dublin facility is a good example of a continuous improvement project by the engineering team. In the CIP process, each item of equipment and pipework is cleaned before the next batch of product is introduced. The cleaning process uses hot water and cleaning chemicals to ensure the required level of cleaning is achieved. With the new CIP process in place, the use of the cleaning chemical was reduced by 83%, water usage by 45% and the time required to complete the cleaning by 43%.
We’ve been focused on sustainability for several years and wanted to better understand how we could accelerate our efforts. We took these findings to heart and are making changes today to further advance our sustainability initiatives in the future.
Shane Doyle
At Alexion’s Athlone facility, the incoming water is required to be purified so it can be used in the manufacturing process. One of the steps in the process is reverse osmosis (RO) where some of the water that goes through the RO unit is rejected. However, this reject water is essentially clean water that can be reused or repurposed. The engineering team looked at different ways to reduce or reuse the reject water settling on installation of a RO recovery skid to purify the reject water so it could be used in the process. This resulted in a 70% reduction in the amount of reject water going to the drain.
Understanding our environmental impact
“To better understand climate change risks, the company also engaged a third-party consultant to conduct a Climate Change Risk Assessment of our major manufacturing sites, contract manufacturers, distribution centres and logistics activities,” Doyle says.
“The assessment considered and ranked potential impacts resulting from the physical effects of climate change, as well as those regarding the global transition to a lower carbon economy. The findings are being used to prioritise actions for improved business resilience over the short, medium and longer term,” he adds.