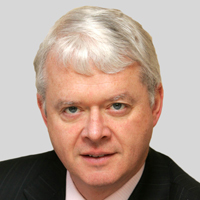
Matt Moran
Two emerging trends are going to influence future expansion of the sector, globally, over the next decade. If Ireland is to retain its leading position, it needs to embrace and excel at these.
The biopharma sector in Ireland continues to expand rapidly. The last decade has seen an estimated €1 billion per year invested in capital. Furthermore, much of this is in state-of-the-art biotech manufacturing.
Digitisation is making biopharma more efficient
Digitisation has made a major impact on all manufacturing since the 1990s. However, now, digitisation is manifesting itself in the biopharma sector.
New, digital technologies are transforming the entire biopharma value chain, increasing flexibility, quality and speed. Previously, the sector has had a long tradition of collecting large amounts of data, mainly for regulatory or quality purposes. But now companies are seeking to use this data to enhance their own efficiency and relative competitiveness.
Both these important developments position Ireland at the forefront.
Smarter working could double companies outputs
This ranges from applying software programmes to reveal true data right the way throughout the manufacturing process and using this to manufacture more smartly. Companies talk of using this to reveal the so-called ‘hidden factory’ and are finding that savings can be substantial, in some cases doubling their output from existing facilities.
At the other end of the range, we see companies looking at applying high-end digital practices to their manufacturing operations. Such practices would allow them to establish virtual platforms, enable points along the supply chain to communicate intelligently with each other, and build intelligent neural networks within parts of their plants. Naturally, given the highly-regulated nature of the sector and the risk profile of the types of products they manufacture, companies will proceed carefully.
Collaboration for testing new applications
The National Institute for Bioprocess Research and Training (NIBRT) has entered into a novel partnership with the biopharma/technology sector. This has been supported by The Boston Consulting Group (BCG) to develop a test bed where such applications can be designed and tested in a non-product-facing environment. This alliance will allow the Irish biopharma sector to keep the revolution in digitisation at the forefront.
Biopharma to follow non-pharma processes of continuous manufacturing
Batch processing traditionally manufacturers pharmaceutical products and their ingredients (known as active pharmaceutical ingredients). There is quality checks for the manufactured batch, as set out in its licence.
An obvious disadvantage of such an approach is that the check is retrospective. for example, if quality attributes are not met, the batch is deemed unsuitable for use – often with significant cost. The non-pharmaceutical chemical industry normally uses continuous manufacturing to generate its products. Currently however, the biopharma sector is looking to employ such technologies for the manufacture of products and ingredients.
Lower costs and smaller carbon footprint
Advantages include real-time control of quality attributes, lower costs and also a lower environmental footprint as these plants are typically smaller and use fewer resources. A number of manufacturers here are developing continuous processes in API and drug product production. Irish contract development company APC specialises in process development in the continuous space.
Both these important developments position Ireland at the forefront, to conclude.